Case study | Automotive Industry
AI VISUAL SYSTEM: Innovative AI system built to train in defect recognition for industrial QA using image recognition and deep learning.
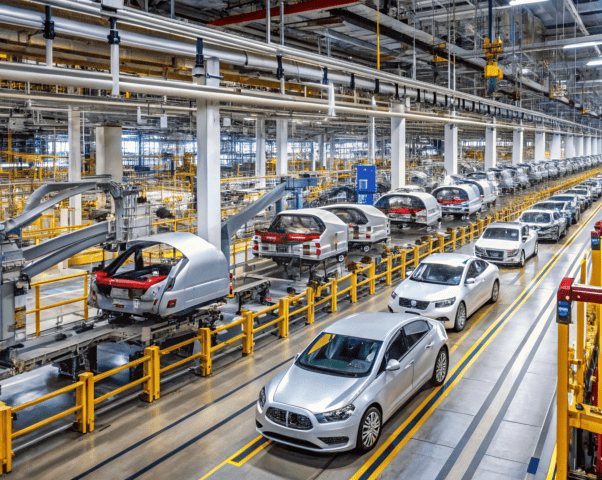
Mission: |
Achieving high accuracy for recognition of defects when deep learning training |

Key Achievements
- The system has achieved a remarkable 98% accuracy in defect identification, reaching the valid limit of deep machine learning training.
- Performing high accuracy rates, particularly on subjects such as holes and missing badges, the system effectively optimises scenarios to minimise false positives– e.g., low light conditions.
- Our client has action plans to execute the AI Visual System factory-wide, covering a range of QA processes in different conditions.
The Challenge
- The primary challenge and innovation lie in the process of refining and adapting the AI Visual System to real industrial environments. This involves addressing issues related to false positives and environment variables, with the goal of creating a reliable, flexible, and high-performing system. Key challenges include optimising processing parameters, as images require significant power, and ensuring sufficient test samples for effective training.
- Currently, the software is being modified to improve visual representations, making it easier to identify defects on vehicle surfaces, vehicle (can be difficult to spot exactly where a dent is on otherwise featureless panels) especially on otherwise featureless panels where dents may be challenging to detect accurately.
- One of the roadblocks faced is the image capture-to-data pre-processing stage, which is being tackled through plans for point-and-click automation to streamline the process.
The Solution
The success of the project has been in the development of software that effectively assist the building of a stable and scalable system. To achieve our goal of identifying and rectifying defects early in the manufacturing process, thereby reducing costs, we have implemented the following actions:
- Adapted and equipped factory stations with QA monitoring and test image providing capabilities.
- Built tools for creating, training, and refining defect models.
- Applied automation technology processes to live conditions.
- Automated QA to detect and flag defects with 98% accuracy.
- Provided the ability to establish and train new defect models, adapting to different environments.
- Industrialised and deployed the solution across the entire factory.
The Technologies
- C# coding
- Deep learning software
- Desktop application interface
- Google TensorFlow (open source)
- HTML — CSS — Vanilla JS
- Microsoft SQL Server (DB engine)
- Microsoft Visual Software
- Mosquitto (MQTT) transmission protocol transmits between separate layers, providing a lightweight method of carrying out messaging using a publish/subscribe model
The Resources
- 1 Project Manager
- 2 AI Data Scientists
- 1 Business Lead
- 6 Business Pilot
- 1 Front End/Back End Developer
The Results
- The comprehensive audit conducted by the team provided the Client with a neutral assessment of their architecture and the maturity of their approach to the implementation of innovative AI system. The recommendations offered not only promoted the successful adoption of the new approach but also led to several other optimisations in their solution.
- By aligning processes with IT resources, the audit enabled more detailed reporting and increased visibility, fostering greater accountability within the organisation. The subsequent phase of the roadmap implemented multiple quality assurance processes across the plant, ensuring sustained high performance and business continuity.
- The development of the AI Visual System involved collaborative efforts of Infotel developers, AI data scientists, business managers, and QA experts. This resulted in the creation and filtering of extensive image banks for training the automated recognition of various repairs, ranging from dents and holes to overpainting and missing elements. The software’s adaptability allows it to adapt to diverse industrial processes like:
- Incorporating variables to fine-tune for different conditions and station sensors.
- Accommodate various defect types.
- Apply alternative deep learning models.
- Potentially extend to anomaly detection and optical character recognition.
- Making use of Infotel expertise in Artificial Intelligence and deep machine learning, the Client uniformly adapted the new system, with a strong priority on automating defect recognition for industrial quality assurance using image recognition and deep learning.